1. Introduction
In order to achieve the desired quality and safety of an electronic product, the quality and safety-relevant functions and properties of the product and its components must be determined and optimized during product development and achieved and maintained during product production. The identification and optimization of these product functions and properties is carried out during product development by:
- defining product functions with measurable performance,
- performing safety analyses of the product design, where these safety analyses always include a Design Failure Modes and Effects Analysis (DFMEA),
- carrying out simulations basedd on physical and data-driven product models, and
- producing and testing hardware prototypes of the product.
Knowing the critical product functions and properties, the identification, optimization and control of production process parameters which influence the critical product properties is achieved by:
- a process safety analysis of the production process (PFMEA),
- AI prediction models for the process parameters, including the specification of setpoints.
- AI predictive models for process parameters including the interpretation of setpoints and specifications.
The quality assurance measures in production are described as a sequence of control steps in the production control plan. The description of each control step includes the methodology used, the equipment and tools applied, as well as the quality and acceptance criteria.
Section 2 describes how quality and safety-related product properties are advantageously identified and optimized in the product development phase. Section 3 shows how product properties and process parameters can be efficiently monitored, optimized and controlled in the production environment. Section 4 outlines the form in which
- automated conformance GmbH and
- Contech Software & Engineering GmbH
provide the described methodologies to their customers.
2. How can quality- and safety-relevant product properties and production process parameters be identified and optimized?
As an example of an application, let's consider the powertrain inverter of an electric vehicle – an automotive safety-critical system whose probability of failure due to hardware faults must be very low. Powertrain failures considered include failures of
- Inverter components,
- detachable connectors and
- fixed joints such as laser welded joints.
As an example, let's take a closer look at the laser welded connections of the busbars in the power section of the inverter. Apart from the operating conditions, the failure rate of these laser welded joints depends largely on selected properties of the laser welded joint, such as the welding depth and geometry. These properties are in turn influenced by about 40 parameters of the laser welding process. A combination of a DFMEA and an analysis of product sample measurements shows that the laser welding process parameters "gap dimension in z-axis", "local heat dissipation during the welding process", "power and reflected power", "weld direction" and "weld transverse offset" are the most important ones due to their variability (and thus high "risk number"). On the basis of statistical experimental design models, measurements are carried out on product samples and optimal values of the production parameters are determined by an engineering AI. These optimal parameter values are then used and validated in the production of further product samples.
Fig. 1 shows the entire process which consists of eight steps.
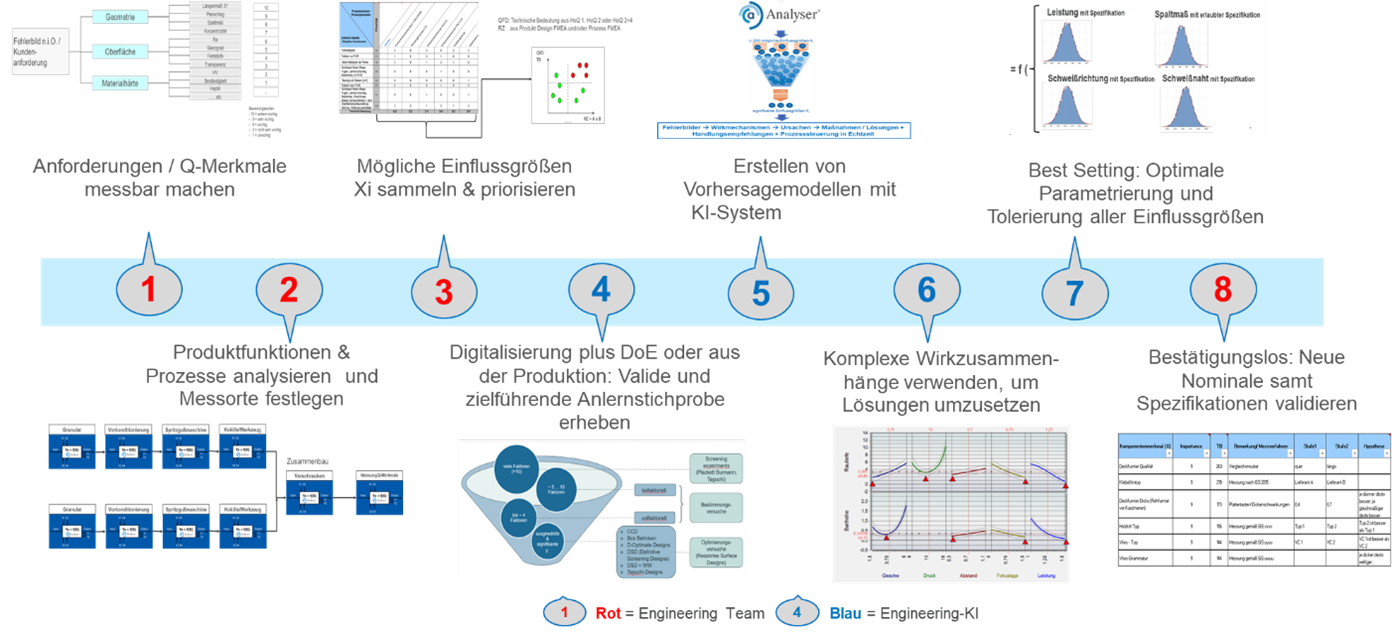
Fig. 1: Eight-step procedure for the identification and optimization of quality- and safety-relevant product properties and production process parameters. © Contech Software & Engineering GmbH, https://www.contech-analyser.de/
3. How to monitor and optimize the parameters of the production process?
During the set-up of the serial production process, the monitoring, control and regulation of the critical production parameters is implemented to ensure the quality and functional safety of the product to be manufactured.
Fig. 2 shows the structure and process of online monitoring and control of production process parameters. It shows how machine data are read out via one or several industrial standard communication interfaces such as OPC UA, Ethernet/IP, Modbus, Profinet, etc., are transferred to a database, and are analyzed in real time by the engineering AI system Analyser® from Contech Software & Engineering. The Analyser® software predicts the production quality and provides the shop floor worker with various kinds of information, such as recommendations for actions, so as to maintain the desired production quality. An online connection of the engineering AI system Analyser® to selected machines can also be implemented, which automatically readjusts critical machine parameters – without any need for intervention by machine operators or workers, see Fig. 2.
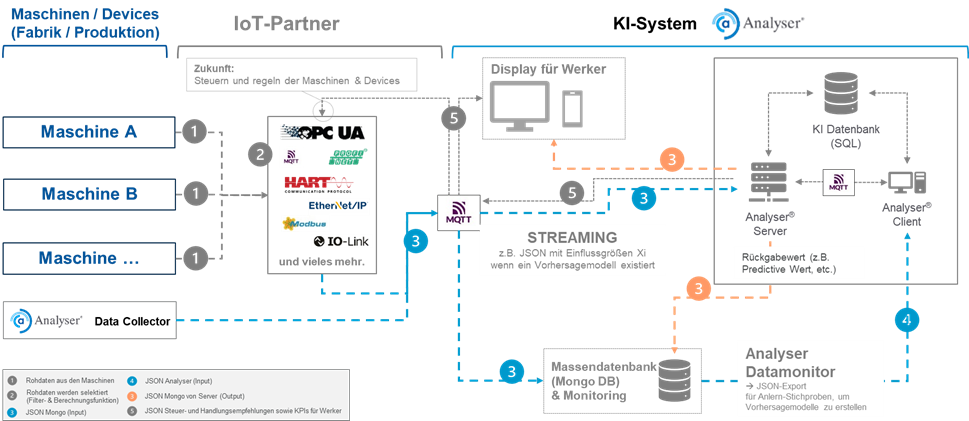
Fig. 2: Online monitoring and control of production process parameters. © Contech & Engineering GmbH, https://www.contech-analyser.de/
Based on occasional test measurements during prodution, the engineering AI Analyser® tells the industrialization engineer
- whether the prediction model is still valid or has to be re-trained;
- whether there could be errors in the measurement equipment so that the production quality and the factors influencing the production quality are no longer predicted correctly, and
- whether checks and possibly also re-calibrations of the measurement equipment are due.
4. Methodology and offer to customers
For the product development and product manufacturing steps described in the previous sections, the companies automated conformance GmbH and Contech Software & Engineering GmbH offer suitable methods, engineering services and software.
automated conformance GmbH have developed the autoConform® methodology and software. Based on this methodology and software, the company offers engineering services for a standard-compliant and fast implementation of all development phases of a safety-critical product. The autoConform® methodology and software enable, for instance the semi-automated creation of technical design, requirements and test specifications; automated visualization and checking of system, hardware and software architectures as well as semi-automated safety and reliability analyses.
Contech Software & Engineering GmbH is an engineering company with its own patented engineering AI system, which ensures robust products and stable industrial processes on the basis of small samples. Contech robustifies a given product design on the basis of physical and data-driven simulations, prototype tests and AI prediction models of the product functionalities, including their setpoints and tolerances. In the industrialization phase, this robust design methodology and engineering AI are used to determine all process parameters with target values and permitted tolerances so as to control product quality consistently in real time during series production. In this way, risks identified in design and process FMEAs are reduced significantly.
Together, the two companies offer a comprehensive range of methods, engineering services and software for efficient and high-quality product development and manufacturing. The combined offering of the two companies enables
- rapid time-to-market of a new or modified product
- with minimal technical risks,
- reduced consumption of energy, materials and resources
- at a lower cost.